How to Recognize What is Porosity in Welding and Improve Your Method
Wiki Article
The Science Behind Porosity: A Comprehensive Guide for Welders and Fabricators
Comprehending the complex mechanisms behind porosity in welding is critical for welders and producers making every effort for impressive workmanship. From the make-up of the base products to the intricacies of the welding procedure itself, a wide range of variables conspire to either intensify or reduce the visibility of porosity.Understanding Porosity in Welding
FIRST SENTENCE:
Assessment of porosity in welding discloses essential understandings into the integrity and high quality of the weld joint. Porosity, defined by the existence of cavities or voids within the weld steel, is a typical issue in welding procedures. These gaps, otherwise correctly attended to, can jeopardize the architectural stability and mechanical residential or commercial properties of the weld, causing possible failures in the ended up product.
To detect and measure porosity, non-destructive screening approaches such as ultrasonic testing or X-ray examination are usually utilized. These methods enable for the identification of inner problems without compromising the stability of the weld. By evaluating the dimension, form, and distribution of porosity within a weld, welders can make enlightened choices to boost their welding processes and attain sounder weld joints.
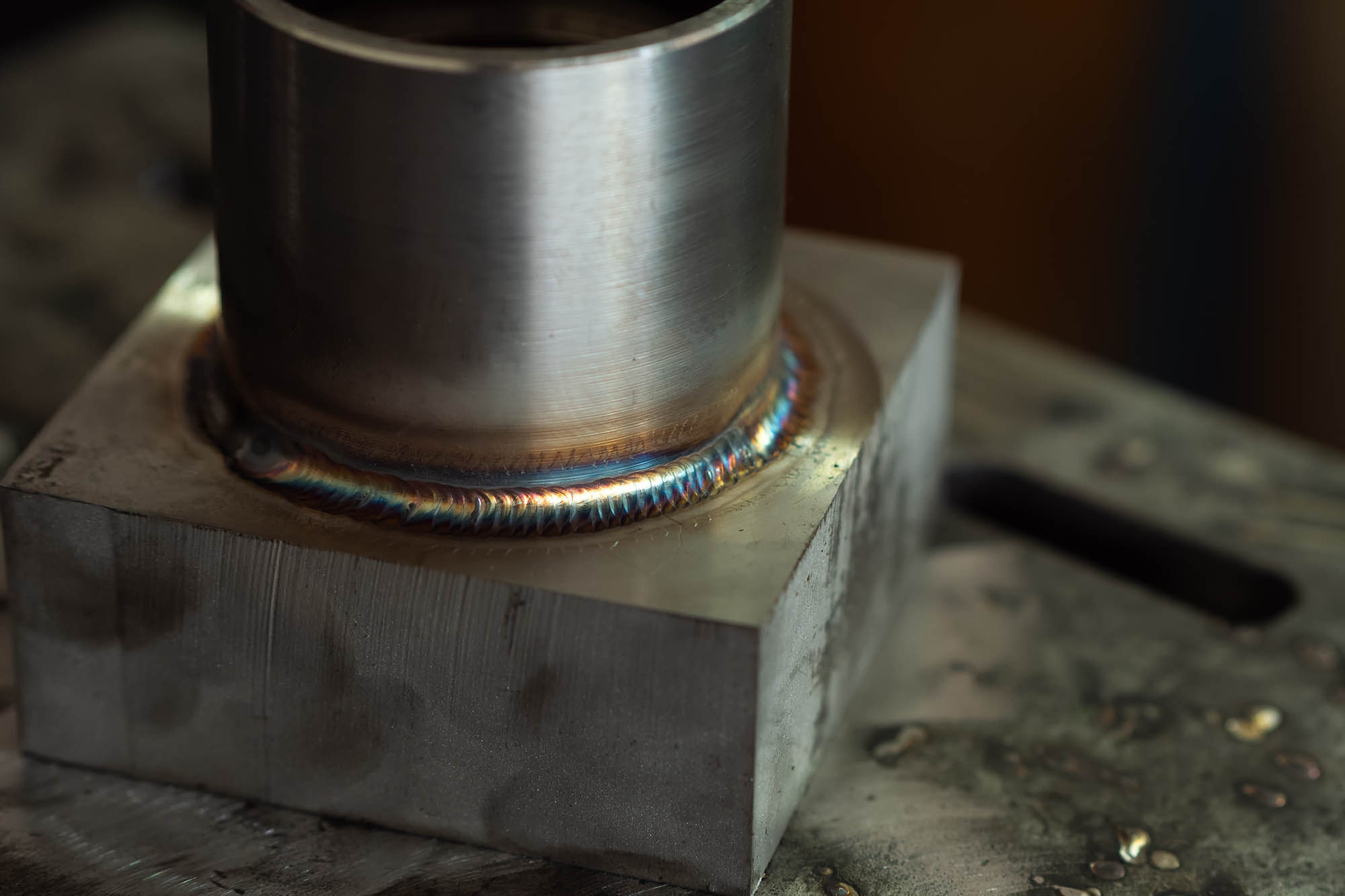
Factors Affecting Porosity Development
The incident of porosity in welding is influenced by a myriad of elements, varying from gas securing effectiveness to the ins and outs of welding specification settings. Welding specifications, consisting of voltage, existing, take a trip rate, and electrode kind, likewise impact porosity development. The welding method employed, such as gas metal arc welding (GMAW) or shielded steel arc welding (SMAW), can influence porosity formation due to variants in heat circulation and gas insurance click coverage - What is Porosity.Effects of Porosity on Weld Quality
The existence of porosity additionally damages the weld's resistance to rust, as the entraped air or gases within the spaces can react with the surrounding environment, leading to degradation over time. In addition, porosity can impede the weld's capability to withstand stress or influence, additional jeopardizing the overall top quality and reliability of the bonded structure. In crucial applications such as aerospace, automotive, or architectural buildings, where safety and sturdiness are vital, the harmful effects of porosity on weld top quality can have serious consequences, stressing the significance of minimizing porosity through correct welding methods and treatments.Methods to Minimize Porosity
Furthermore, making use of the proper welding parameters, such as the proper voltage, current, and travel speed, is critical in preventing porosity. Maintaining a consistent arc size and angle throughout welding additionally helps reduce the possibility of porosity.
Utilizing the suitable welding strategy, such as back-stepping or using a weaving movement, can also aid disperse warmth uniformly and decrease the possibilities of porosity formation. By executing these techniques, welders can properly lessen porosity and generate high-grade bonded joints.

Advanced Solutions for Porosity Control
Executing advanced modern technologies and More Help ingenious approaches plays an essential duty in achieving remarkable control over porosity in welding processes. Additionally, using sophisticated welding techniques such as pulsed MIG welding or modified ambience welding can likewise aid mitigate porosity problems.An additional advanced service includes using advanced welding equipment. Utilizing equipment with built-in functions like waveform control and sophisticated power resources can boost weld top quality and lower porosity risks. Additionally, the execution of automated welding systems with precise control over parameters can dramatically decrease porosity issues.
In addition, including innovative surveillance and examination modern technologies such as real-time X-ray imaging or automated ultrasonic screening can help in spotting porosity early in the welding why not try these out process, enabling instant corrective actions. Overall, incorporating these innovative options can substantially boost porosity control and boost the general high quality of welded parts.
Verdict
In conclusion, recognizing the science behind porosity in welding is crucial for welders and producers to produce top notch welds - What is Porosity. Advanced remedies for porosity control can better improve the welding procedure and guarantee a solid and reputable weld.Report this wiki page